Revolution Lighting Technologies
Who: Director of Engineering
Where: Westlake Village, CA
When: April 2009 - May 2022 (13 years, 1 mo)
What: Oversaw design/sourcing, development, testing, manufacturing, configuration, and sustaining activities for over 30,000 unique solid-state light-emitting diodes (LED) lighting products sold to retail, energy service contract organizations (ESCOs), and wholesale outlets for both domestic and international commercial retrofit and new construction markets. Orchestrated operations of product design, manufacturing processes & procedures, cost & budget analyses, design review meetings, quality control, quality assurance, corrective action reports, technical and other company-related information to and from over 80 different domestic and overseas contract manufacturers and suppliers according to ISO9001:2015, FAA, and Mil-Std requirements for various product lines. Supervise patent search, patent development, intellectual property/copyright management, royalty license program, trademark maintenance, and other legal matters related to proprietary product technology and manufacturing information. Directed testing and certification of RVLT products to ensure they meet safety, regulatory, and utility standards. Administered content for training, website, and technical documentation to provide support for customers, distributors, dealers, and salespeople.
Designed and implemented product engineering and management processes and systems such as part numbering convention, part entry into ERP system, QA/QC, test, & compliance protocols to properly document and support products for improved quality, compliance, accounting, quality, and performance consistency assurance.
Crafted document control processes and templates for all product documentation such as spec sheets, installation instructions, warranty, white papers, application notes, tech bulletins, build instructions, bill of materials, etc.
Set up consistent and sustainable systems and protocols to facilitate more than 100 tickets per month pertaining to technical, application, and product returns (RMA) and on-site support for customers and department operations to determine fault and customer application repair, improvement, and compensation solutions.
Mentored, focused on meeting purposes and agendas, and encouraged cross-training to foster growth in employee and contract manufacturer/supplier relationships to improve and grow business strength resulting in responsibility redundancy and multi-discipline thinking and application of knowledge.

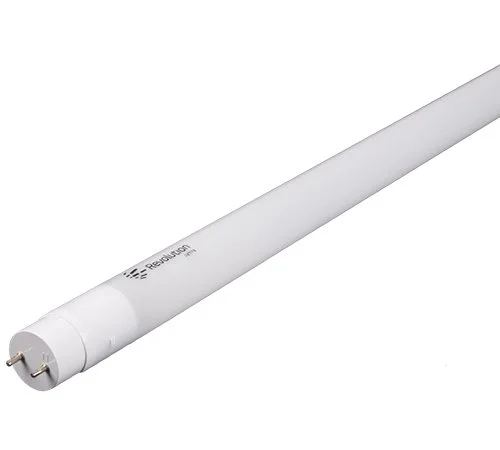
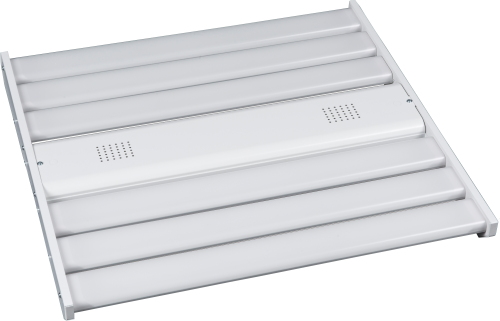